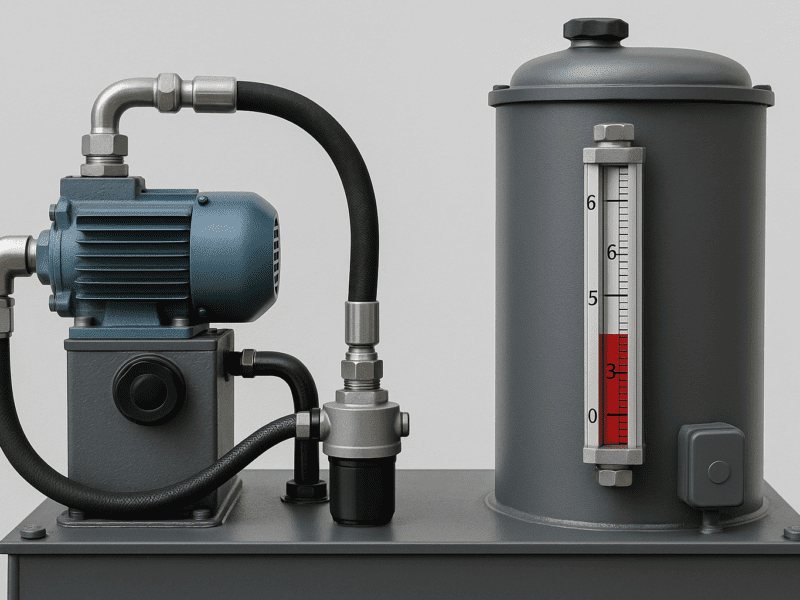
Introduction
We admit it – we like power tools. Like many folks who work in technical fields, appreciating tools used to build great
works feels the same as appreciating a talented artist’s paintbrush. As much as we’re drawn to everyday power tools,
we have an even greater level of respect and awe for hydraulic tools as bigger, stronger, more powerful versions of
anything you’d find in our garages at home. Hydraulic construction tools such as jackhammers and cut-off saws
operate at extreme pressures and forces, tackling heavy-duty projects all throughout industrial spaces. With such
power comes inherent risks as well, most notably when hydraulic tools suffer from interruptions in their fluid supplies,
which can lead to unsafe, rough operation and even complete tool failure. Knowing these risks firsthand, a premier
hydraulic equipment manufacturer recently engaged Whitman to discuss adding automated safety features to their
portable hydraulic power packs. We weren’t sure if we’d get our hands on any hydraulic tools ourselves during this
project, but any chance to automate away safety concerns was reason enough to dive in.
About Us
As a veteran-owned small business, Whitman Controls is dedicated to supplying premium quality, reliable,
technologically advanced instrumentation for use in nearly any application. Our Bristol, CT manufacturing facility
embodies over 40 years of engineering, fabrication, and customer service expertise, serving both end-user and
manufacturing customers nationwide through direct and distribution channels.
Application Summary
Portable hydraulic power units are self-contained packages commonly comprised of an internal combustion engine (or
electric motor), a hydraulic pump, a hydraulic fluid reservoir, and a hydraulic fluid distribution manifold with valves
and control devices. These power units look very similar to portable electrical generators, but instead of generating
electricity, they generate high-pressure hydraulic fluid flows used to drive external tooling and equipment.
Based on the principles of hydraulic fluid power, these power packs’ relatively small engines can create substantial
hydraulic forces – a typical hydraulic power pack lineup spans 5 to 30 horsepower motor sizes, which can create 8 to
20 gallons per minute of hydraulic flow up to 2,500 PSI. Anywhere that a portable hydraulic tool is called for, the
portable hydraulic power pack is needed to power that tool – demolition, steel erection, equipment rigging, vehicle
towing and recovery, and maintenance in industrial, marine, aviation, and agricultural fields are just a few examples.
Challenge
Safety is a major concern when it comes to hydraulic fluid power systems, given the very high temperatures,
pressures and forces involved. As a manufacturer of portable hydraulic power units used in heavy industrial
environments, our client on this project knew these safety concerns well, so well in fact that this project was
specifically created to address safety risk factors identified through a recent end-user experience survey.
In this survey, our client asked end users to describe the most common functional problems that they experienced
with hydraulic power packs from any OEM. After analyzing all the great feedback received, our client distilled the
concerns down to two root causes:
● Inconsistent Tool Performance due to Air Entrainment – When air enters a hydraulic fluid power circuit,
that air causes a drastic reduction in the power transmitted to the tool and the consistency of its operation.
With air being compressible (and hydraulic fluid being incompressible), any amount of air that makes its way
into a hydraulic cylinder, hose, or tool can cause the device to lurch, stall, operate slowly, and generate
excess noise.
● Complete System Failure due to Empty Hydraulic Reservoirs – If a hydraulic power pack runs out of
hydraulic fluid during operation, connected tools and components can suddenly fail. Once a hydraulic pump
loses prime, the circuit’s flow and pressure will instantly drop, which can, in turn, cause any hydraulic
component under load to drop as well.
Fully recognizing the safety hazards embodied in these two functional concerns, our client resolved to add safety
devices to their hydraulic power packs that would protect against these situations from occurring. The client knew that
automated sensors were likely the solution they were looking for and requested our application engineering team to
have a look.
Quote
“When we polled our customers, the two biggest risk factors they reported were the reservoir [on our hydraulic power
packs] running low enough to suck air into the circuit, or the pump stalling because fluid ran completely out. That’s
how we knew we needed to add controls to monitor our systems, which we thought was going to be a really
complicated process, but Whitman made it super easy.” -Product Manager, Confidential Hydraulic Power Unit OEM
Solution
The two main problems that needed to be solved on this project involved air getting into the hydraulic circuit, both of
which pointed to the hydraulic fluid reservoir as the place to start our evaluation. After a short review, it became
apparent that both issues were two halves of the same concern: insufficient hydraulic fluid level in the reservoir,
leading to air entrainment or complete pump stall-out. Our engineers ran with the idea of controlling reservoir level
as the solution, and wrote out three suggested new functional features to run by the client:
● Low Level Protection – When low level is detected in the hydraulic fluid reservoir, the power pack should
sound an annunciator to warn operators. This condition can occur when leaks, long hydraulic hoses, and large
tool bores draw a higher amount of fluid from the system than anticipated. In addition, this scenario can
result from a partially full reservoir level sloshing below the pump suction line, causing intermittent breaks in
fluid flow that pull in air.
●Safety Cut-Out – When a low level is detected in the hydraulic fluid reservoir, the power pack should enter
an emergency stop condition, closing valves to maintain system pressure and sounding a unique alarm
annunciator tone to warn operators. System operation should be held in the current state until the low-low
level condition is cleared. This condition can occur anytime the reservoir loses so much fluid volume that
there is not enough remaining to ensure safe tool operation.
●High Level Protection – When high level is detected in the hydraulic fluid reservoir, the power pack should
sound an annunciator to warn operators. This condition can occur when hydraulic fluid supply and return
flows become unbalanced, when high temperatures cause thermal expansion of the fluid, and when undrained
tools are connected and excess fluid flows back into an already topped-off reservoir. While this feature wasn’t
part of the original concerns, our engineers suggested adding this functionality as it uses the same sensor and
incurs negligible extra cost.
To achieve the above three new functions, Whitman suggested a multi-point level switch assembly to be installed into
the hydraulic power packs’ reservoirs. A multi-point level switch consists of multiple level floats installed onto a
singular center shaft, each at a different elevation. When fluid hits each level float, the float is raised and the internal
electrical switch is cycled, completing an electrical circuit back to relay inputs on the hydraulic power pack’s control
board. From bottom to top, three floats would be installed for low-low level, low-level, and high-level switch points,
providing discrete input feedback to the controller as each level was met.
To round out our recommendation, we suggested the Whitman Controls’ L30 Series Multi-Level Switch sensor based
on the following features:
Custom-Configured Multi-Point Level Switch Design
1-1/2″ NPT Threaded Connection for Top or Bottom Mounting
Single Brass Shaft with up to Five Buna Level Switches
Compatible with Hydraulic Oil up to 230°F
Submersible Potted Floats rated to NEMA 6
Minimum Liquid Specific Gravity of 0.70
Maximum System Pressure of 180 PSIg
50vA Electrical Switch Rating
SPST Dry Reed Switches, NO or NC
Up to 48″ Overall Length
ISO 9001 Certified Manufacturing Process
Results
Our client took our recommendations to their product management team, seeking confirmation that the suggested
level switch and new controller functions would address all their needs. At the same time, the client spoke with a
handful of the original survey respondents to get their feedback on the newly proposed safety features. Within a few
weeks, both conversations came back with resounding affirmation that the suggested level control solution was the
right path to take. As of this writing, our client has incorporated the Whitman L30 Multi-Level Switch into about half
of their hydraulic power pack unit models, with the remainder of their catalog set to receive the upgrade by the end of
the year. And even though we didn’t get our hands on any hydraulic power tools during this project, we watched
enough videos to know we should leave that kind of power to the pros!
Data Bullets
- 100% reduction in hydraulic tool failure due to the reservoir running dry
- 600+ hydraulic fluid safety accidents in North America per year
- 20% improvement in power pack maintenance costs thanks to avoiding air entrainment
- 2-3 weeks’ lead time on custom multi-level sensors
Here at Whitman Controls, our values drive us to provide the highest level of servant partnership that you can find.
To discuss your applications or to learn more about our capabilities, please contact us at (800) 233-4401 via email at
info@whitmancontrols.com, or online at www.whitmancontrols.com.