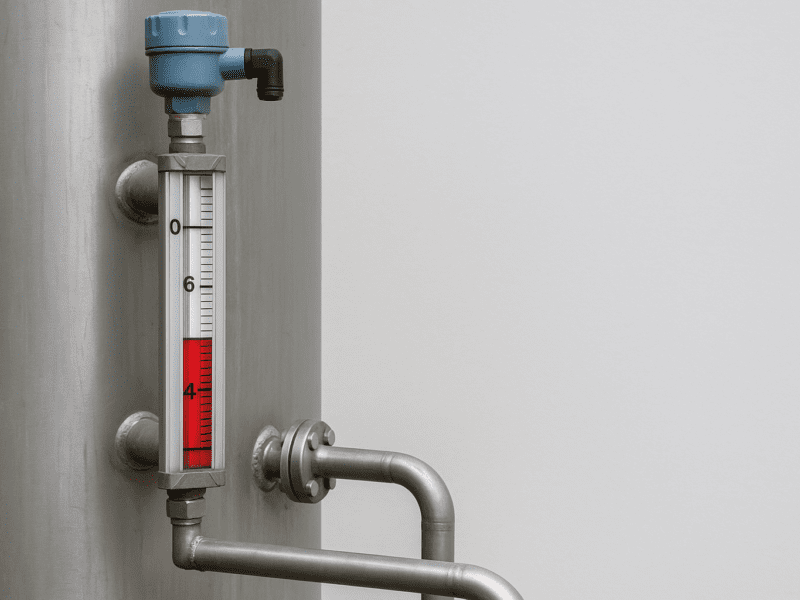
In comparison to the previous sensor types that we’ve covered in our Instrumentation 101 series, level sensors are easily the most diverse and intricate of the bunch. In modern process controls, level sensors are used to quantify the amount of material present within a three-dimensional space across a wide range of operating principles and design types. Adding to this complexity, level sensors can be used on practically any type of material as well. To help readers get their bearings, we’ll break down the massive topic of level sensors into digestible chunks below, including application examples and key purchasing considerations.
To begin, let’s establish a working definition of level sensing technology with these statements:
● Strictly speaking, level measurement takes the vertical dimension of a material housed within a container. For example, we could describe a fluid tank as containing a level of “5 feet of water”.
● Level measurement does not have a native unit of measure. Feet, inches, and meters are commonly used to describe the material’s height, as a percentage of the total available level. For example, with a 10-foot-tall tank, a 5-foot water level would equate to a 50% full level.
● Level can only be measured relative to a reference point (such as the bottom of a tank), and unless we’re measuring sea level has no universal reference point.
● In general, level can only be derived in one of three ways: by physical presence, inferred by weight, or inferred by head pressure.
● Level is most often measured in different units than those presented to operators. For example, a hydrostatic level sensor may physically measure in inches of water column, but display a calculated value to operators in gallons.
● For these reasons, physical level and calculated level values are easily confused. In practice, level, volume, mass, and weight values are used interchangeably.
Level Sensor Styles
Even though level sensors come in a wide array of styles, all have three main parts: a sensing element that physically detects the material being measured, a mechanism that translates this sensed condition into a usable value, and an output device that communicates this value to operators. Next, we’ll identify the main styles that these three parts can be configured into:
● Level Sensor – The term “sensor” describes any type of device that can sense and communicate level readings, and is a generic term for any of the below specific instrument designs.
● Level Gauge – A level gauge is a mechanical device that physically measures a level value and provides a visual, real-time readout. Gauges are the most basic form of instrument, requiring operators to manually read the gauge and make process control decisions accordingly.
● Level Switch – A level switch provides simple automated control functionality by opening and closing an electronic circuit when level values hit a preconfigured setpoint. Switches are available in either mechanical or solid-state relay forms, providing a discrete on/off electrical signal output referred to as point level measurement.
● Level Transmitter – Level transmitters contain advanced electronics that produce an analog current output signal (i.e., 4-20mA). This current output is scaled to the desired level range, allowing very precise signal resolutions that can carry long distances. Transmitters provide continuous level measurement, which means that level readings are produced nonstop at any point across the sensor’s range.
● Level Transducer – Level transducers produce an analog voltage output signal (i.e., 0-10V). This voltage signal is scaled to the desired level range and is best for short, low-noise wiring installations, given its sensitivity to power quality fluctuations. Like transmitters, transducers provide continuous level measurement.
Level Sensor Operating Principles
The above list of level sensor types describes a packaged sensor and how it communicates its readings to operators, but it doesn’t describe the actual sensing technologies employed. So, let’s next review the most common sensing technologies:
● Physical Gauging – Implies that a device is used to physically contact the material being measured so that its level can be quantified. Forms include viewing windows, dip sticks, calibrated gauge tubes, floats, magnetic slides, weighted paddles, etc. Supports both point and continuous level measurement.
● Weight – Though technically a separate instrumentation category, weight via load cells or scales is commonly used to infer level in solid and liquid materials.
● Conductivity – Uses a material’s ability to conduct electricity. When the material contacts the conductive sensor, an electrical current path is created that triggers a point level relay.
● Vibration – Mainly used in bulk solids storage. A vibratory point level sensor detects material contact through changes in vibrational frequency of a fork.
● Hydrostatic Pressure – Works on the principle of hydrostatic head pressure at the bottom of a fluid column. Increasing fluid height increases pressure, used for both point and continuous level values.
● Differential Pressure – Detects differences between a fluid’s pressure and a reference pressure to provide point or continuous level data.
● Capacitive Sensing – Based on changes in capacitance caused by material enveloping a capacitor. Works for both point and continuous measurements.
● Inductive Sensing – Based on inductance; only works with metallic materials for point-level measurement.
● Non-Contact Wave Sensing – Uses electromagnetic waves (radar, ultrasonic, microwave) to measure levels without physical contact. Suitable for both point and continuous measurements.
Level Sensor Applications
Level sensors are used wherever measuring material level benefits operation, performance, or safety. Application examples by principle include:
● Physical Gauging – Used in simple, low-cost setups where physical contact is acceptable, e.g., river buoys, wastewater tank floats, sulfuric acid gauges.
● Weight – For non-homogeneous or stratified fluids and solids, e.g., sugar slurries, raw milk, tar, sand.
● Conductive Level – Ideal for basic, responsive switching with conductive fluids, e.g., boiler feedwater tanks, chemical day-use tanks.
● Vibratory Level – Bulk material storage, e.g., grain bins, crude oil tank overfill protection.
● Hydrostatic Pressure – Used in applications with consistent fluid density, e.g., fuel tanks, pilot chemical reactors.
● Differential Pressure – Suited for sealed or hazardous systems, e.g., dairy evaporators, nitrogen vessels.
● Capacitive Level – Dual-purpose: point level detection or advanced continuous measurement in mixed-phase fluids.
● Inductive Level – Point-level detection in magnetic materials, e.g., molten steel, metallic coatings.
● Non-Contact Wave Level – Preferred for uneven settling or mixed solids, e.g., grains, powders, clays.
Key Considerations When Selecting Level Sensors
Choosing the right level sensor requires evaluating several technical factors:
● Sensor Rating – Should cover the full range of expected level values plus additional headroom.
● Spike and Peak Ratings – Must tolerate temporary overfill or pressure spikes without failure.
● Temperature Rating – Exceeding rated limits can skew sensor accuracy or calibration.
● Enclosure Rating – Protection standard for internal electronics (e.g., NEMA 4X / IP66).
● Accuracy and Repeatability – Describes deviation from actual level and variation in repeated readings.
● Housing Material – Must be compatible with environmental conditions; options include stainless steel, aluminum, plastic, etc.
● Wetted Material – Materials that contact the fluid (e.g., diaphragm, seal); must be chemically compatible.
● Electrical Connection – Hardwiring is more reliable; quick-disconnects offer easier maintenance.
● Fluid Connection – Must match system design; includes NPT, BSP, flanged, JIC, SAE types.
● Cycle Time – Indicates how often a switch can change states. Too low a cycle time leads to missed events or early failure.
● Certifications and Approvals – Depending on the application, look for UL, CSA, or industry-specific approvals.
As a veteran-owned small business, Whitman Controls is dedicated to supplying premium quality, reliable, technologically advanced instrumentation for nearly any application. Our Bristol, CT manufacturing facility embodies over 40 years of engineering, fabrication, and customer service expertise, serving both end-user and manufacturing customers nationwide through direct and distribution channels.
Our values drive us to provide the highest level of servant partnership that you can find. To discuss your applications or to learn more about our capabilities, please contact us at (800) 233-4401, via email at info@whitmancontrols.com, or online at www.whitmancontrols.com.