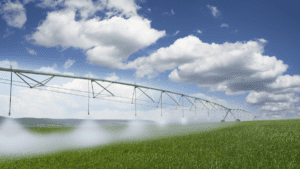
Alternative Energy
Most energy consumed by humans across the world comes from oil, coal, and natural gas – all of which are finite resources. The need for alternative fuel sources is unprecedented, both to fulfill ever-increasing demand as well as to reduce fuel-burning environmental burdens at a global scale. Wind, geothermal, solar, hydroelectric, biodiesel, hydrogen, and biomass energy sources are our current most viable options, and advanced process control instrumentation plays a significant role in supporting these technologies as they scale up.
CHALLENGES
Few other market segments combine economic, infrastructure, regulatory, and process control demands all in the same discussion as Industrial Alternative Energy does. Navigating the myriad of technical challenges found in these applications takes a watchful eye on overall system design and operation, all in the context of providing safer, renewable energy for generations to come.
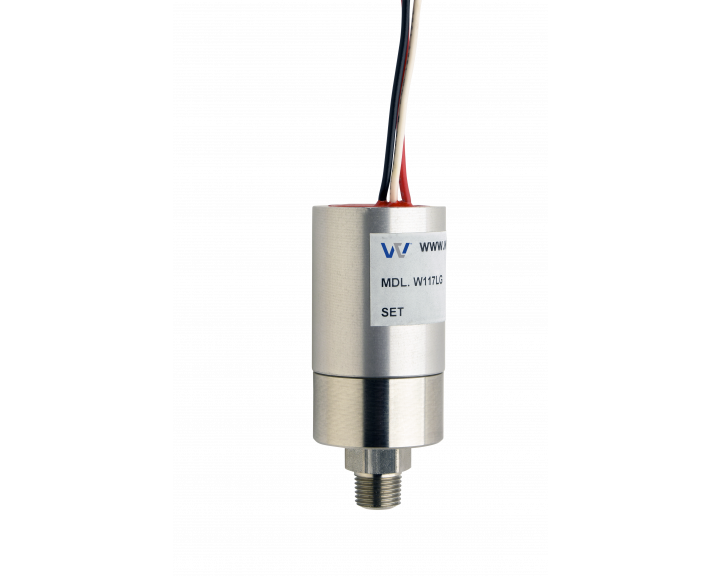
EMERGENT, HIGHLY CUSTOMIZED APPLICATION
➤ Large-scale Alternative Energy processes are still in their infancy and in many ways, every new installation is a further customized and refined iteration of the last. This drives a dichotomy of sorts – that technology selections should be economical in nature since they may change as the process evolves, while also being incredibly reliable as you’d expect from critical infrastructure.
HARSH ENVIRONMENTAL CONDITIONS
➤ Scorching deserts, windy mountain ranges, remote ocean shores, and desolate geothermal valleys make up the common locations that sizable Alternative Energy installations occur. In these conditions, process control instrumentation must perform without fail and for long periods of time, especially in the case of safety and emergency control loops.
FUNCTIONAL INEFFICIENCIES
➤ By default, Alternative Energy sources suffer from functional inefficiencies that impact their performance – very low output efficiency, very high deployment costs, intermittent and widely variable output, high maintenance costs, and remote installation locations all present challenging nuances towards their process controls.
SOLUTIONS
Alternative Energy is not simply a buzzword, but an economic reality that the world must contend with in order to supply the energy and environmental compatibility future generations will rely upon. With this goal in mind, Whitman Controls has instrument models that serve the specific cost, resilience, and integrity interests of our Alternative Energy customers.
Conventional Solutions to Emergent Applications
While an application may be novel in its field, diligent engineering review often finds that a standard or semi-standard solution can be made up by piecing together conventional components – the magic being in the way these components are applied and configured. Our experienced engineers can help break down complex, emergent projects to help you navigate options between standard and custom instruments.
ISO Quality Control
Our product quality may speak for itself, but how can we assure this before you put our instruments into use? Whitman Controls is an ISO 9001 Certified business, providing you with the assurance that our products are entirely designed, manufactured, tested, and delivered using third-party verified practices, complete with total process documentation, material traceability, and chain of custody control.
Simplified Standardization
Our product catalog includes a wide range of solutions that span in-process as well as central utility applications, and everything in between. Standardizing on a common instrument manufacturer across multiple areas of a plant vastly simplifies procurement, maintenance, troubleshooting, and support, not to mention new project developments – benefits that are especially pertinent to large, complex manufacturing sites.
Full Product Customization and Value-Add
Our predefined product catalog of hundreds of instruments is only the tip of the iceberg here at Whitman Controls. We can fully customize virtually any of our product models to your exact needs. We're especially excited about emergent applications and highly technical challenges, and can help you with one-off R&D samples as well as high volume production runs of your World's First instrument design, plus custom wiring harnesses, adaptors, and kits.
ALTERNATIVE ENERGY APPLICATION
PRODUCTS
Whitman Controls offers multiple instrument, switch, and transmitter models that are engineered to match the demands of the Alternative Energy Industry, such as these below related products.
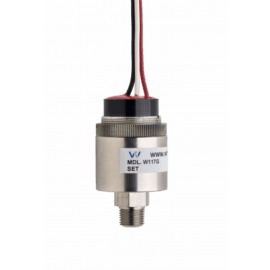
W117G Ultra Pure Pressure Switch
The W117G Ultra Pure Stainless Steel Pressure Switches have all welded stainless steel interiors which are Helium leak checked to pass 4 x 10-9 Std CC/Sec. These switches are used in silicon wafer ovens, numerous medical devices and other applications where even the slightest impurities are not tolerated.
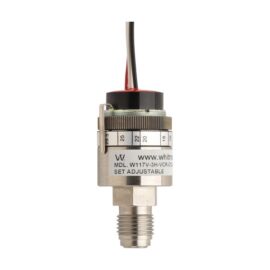
W117V Ultra Pure Stainless Steel Vacuum Switch
The W117V Ultra Pure Stainless Steel Vacuum Switches have all welded stainless steel interiors which are Helium leak checked to pass 4 x 10-9 Std CC/Sec. These switches are used in silicon wafer ovens, numerous medical devices, and other applications where even the slightest impurities are not tolerated.
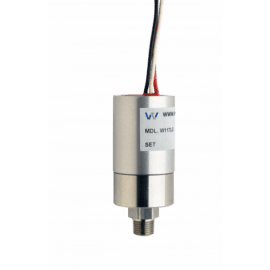
W117LG - Ultra Pure Long Body NEMA 4 Pressure Switch
The W117LG NEMA 4 Ultra Pure Stainless Steel Pressure Switches have all welded stainless steel interiors which are Helium leak checked to pass 4 x 10-9 Std cc/sec. These are the NEMA 4 rated weather-proof, liquid-resistant version of the W117G, suitable for out¬side applications or in areas of condensing humidity.
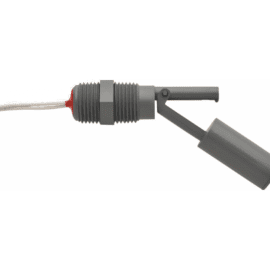
L20 CPVC Liquid Level Switch
The L20 Series Side Mounted CPVC Plastic Liquid Level Switches are typically used in water and potable water applications. The side mount provides added versatility, allowing the switch to be used as a high or low level indicator, and plastic body provides use up to 100 PSI.
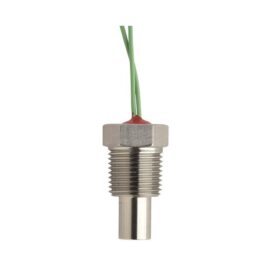
TP Series Economical Stainless Steel Temperature Probe Switch
The Whitman Controls TP Series Economical Stainless Steel Temperature Probe Switches are a creep action thermostat/thermal protector switch providing almost no differential between opening and closing temperatures. The switch is designed for use from 50˚F to 250˚F in 25˚F increments with a +/-5˚F tolerance. Special temperature ranges and configurations are available for OEM customers.
KEY APPLICATIONS